Introduction
EVA foam beach bags have become indispensable accessories for beachgoers due to their combination of durability, lightweight nature, and customizable designs. This comprehensive guide explores the intricate manufacturing process behind these bags, highlighting the integration of advanced technology with meticulous craftsmanship to meet high standards of quality, functionality, and environmental responsibility.
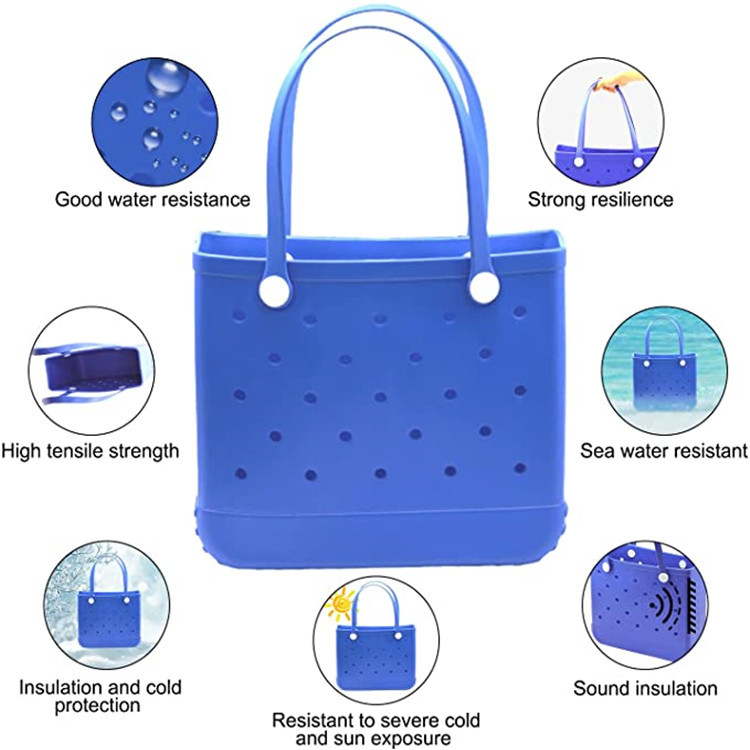
Key Steps in the Manufacturing Process of EVA Foam Beach Bags
Criteria for Material Selection: Discuss in-depth the specific criteria used for selecting EVA foam sheets, including how density affects durability and flexibility, how thickness consistency impacts manufacturing uniformity, and considerations for environmental sustainability such as recyclability and eco-friendly production processes.
Types of EVA Foam: Explore different types of EVA foam available in the market, highlighting variations in properties and applications (e.g., closed-cell vs. open-cell foam, different grades of hardness).
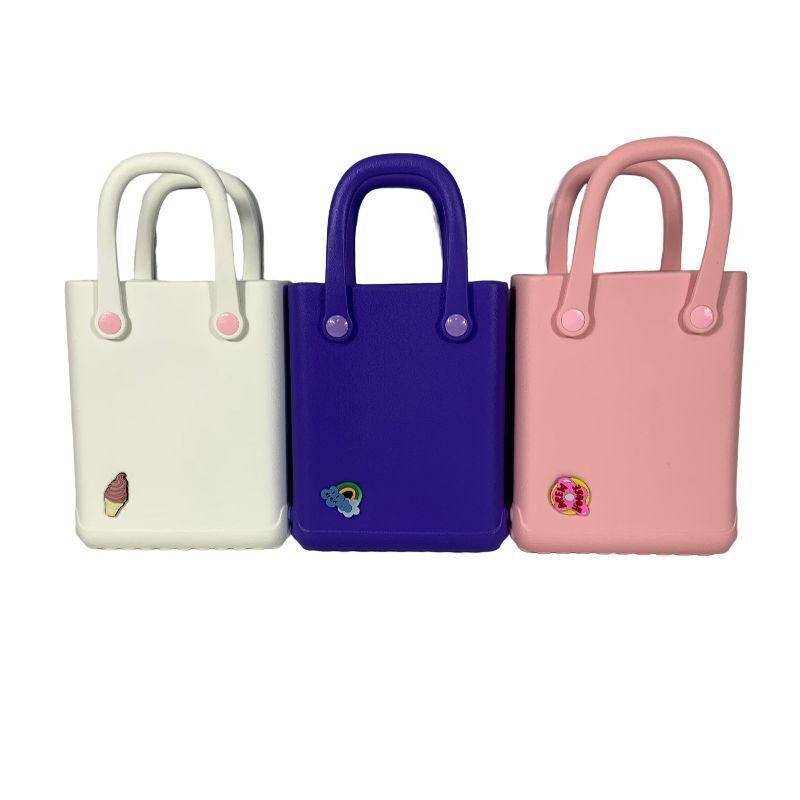
Design and Prototyping
Market Trends: Explore current trends in beach bag designs, including popular colors, patterns, and features preferred by consumers. Discuss how these trends influence the design process and product development strategies.
Prototyping Process: Detail the stages involved in prototyping, from initial concept sketches to 3D modeling and digital rendering. Highlight the importance of prototyping in refining design elements such as ergonomics, usability, and structural integrity.
Foam Production and Molding
Foam Manufacturing Techniques: Explore different methods used in EVA foam production, such as injection molding, compression molding, and extrusion. Compare the advantages and disadvantages of each technique in terms of production efficiency, material utilization, and product quality.Quality Control in Molding: Discuss quality control measures implemented during the molding process to ensure consistent foam density, thickness, and structural integrity. Highlight the role of automated systems and real-time monitoring in maintaining manufacturing standards.
Advanced Materials: Investigate advancements in EVA foam technology, including innovations in additive manufacturing (3D printing) and hybrid materials (e.g., foam composites). Evaluate their potential impact on product performance and customization capabilities.
Cutting and Shaping
Precision Cutting Techniques: Explore advanced cutting technologies employed in the industry, such as laser cutting and water jet cutting. Compare these techniques in terms of speed, accuracy, and suitability for different types of EVA foam materials.
Complex Shapes and Patterns: Discuss challenges and solutions related to cutting complex shapes and intricate patterns in EVA foam, including the use of CAD software for digital modeling and toolpath generation.
Assembly and Bonding
Adhesive Technologies: Explore different types of adhesives used in EVA foam assembly, including solvent-based adhesives, hot melt adhesives, and reactive adhesives. Discuss their bonding mechanisms, curing processes, and applications in various environmental conditions.
Heat Bonding Techniques: Detail the process of heat sealing and welding in EVA foam assembly, highlighting equipment and temperature control methods. Discuss advantages such as enhanced seam strength and waterproof properties.
Finishing and Customization
Surface Coatings: Explore types of surface treatments applied to EVA foam, such as polyurethane coatings, silicone coatings, and nanotechnology-based hydrophobic coatings. Discuss their impact on durability, aesthetic appeal, and environmental sustainability.
Embossing and Printing Techniques: Detail methods for embossing logos, textures, and patterns onto EVA foam surfaces, including heat embossing and screen printing. Discuss advancements in digital printing technologies and their application in customizing designs.
Quality Assurance and Testing
Quality Control Standards: Explore industry standards and certifications related to product quality and safety, such as ISO 9001 and REACH compliance. Discuss the role of quality management systems in ensuring consistency and reliability in manufacturing processes.
Durability Testing: Detail methodologies for conducting durability tests on EVA foam beach bags, including abrasion resistance testing, tensile strength testing, and impact resistance testing. Highlight the significance of these tests in predicting product lifespan and performance under different usage scenarios.